Gojeep
Well Oiled
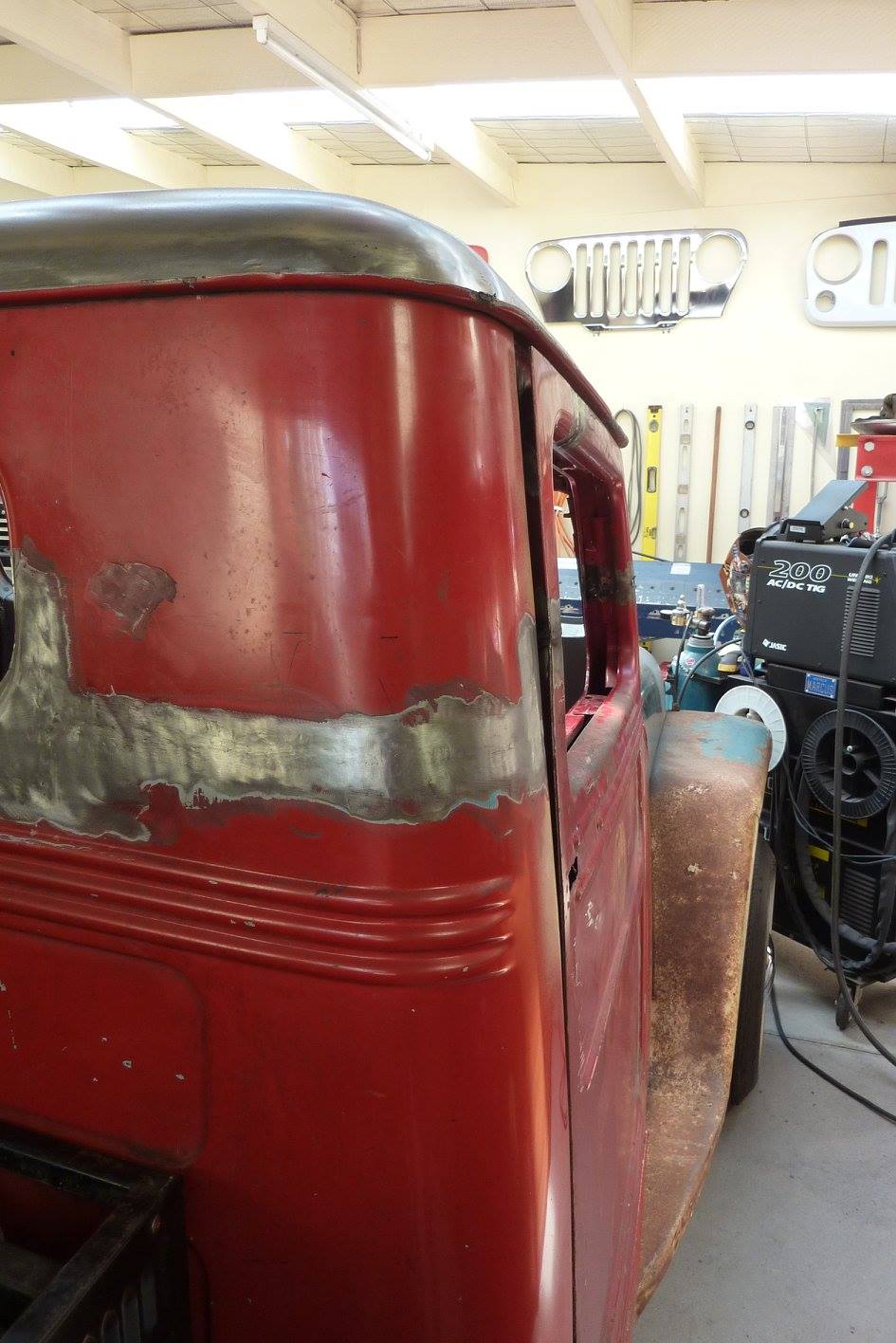
After doing all the adjusting I could on the hinges and forcing the top of the frame over, it was still hanging outwards at the top if the rest of the door was in line.
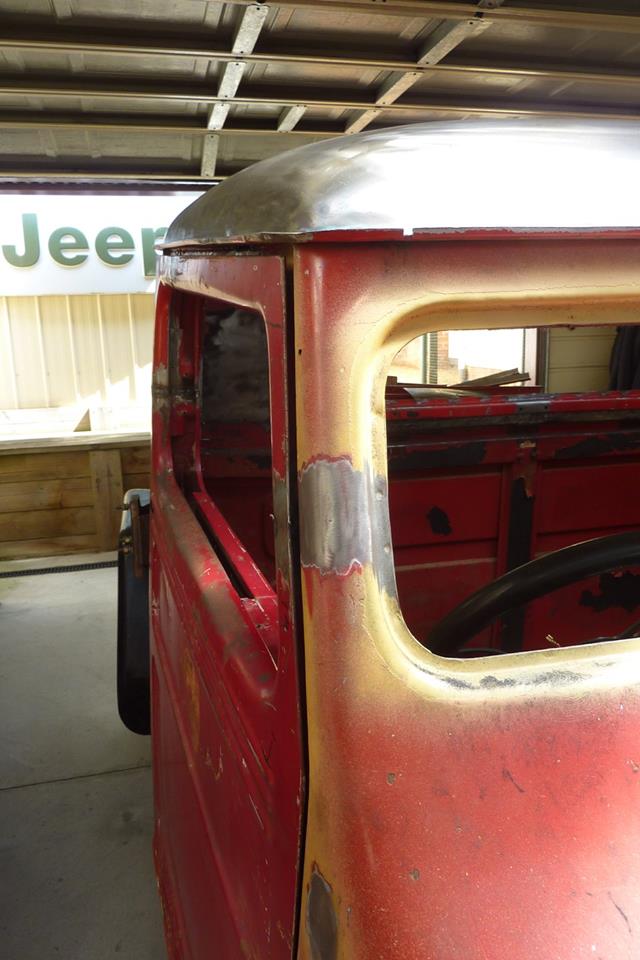
The front was the same although not as bad.
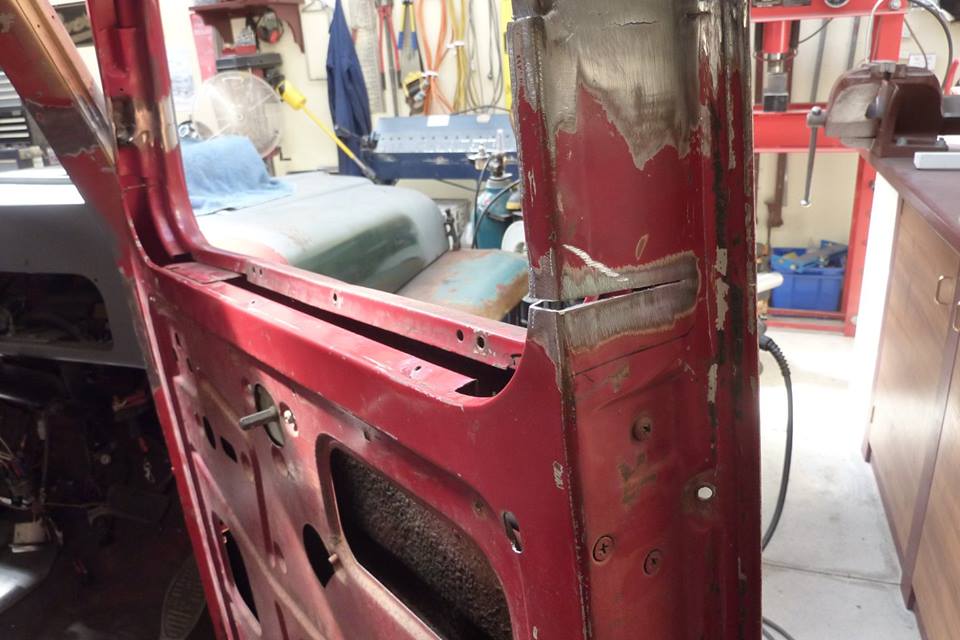
A wedge was cut into the frame where the bend was needed.
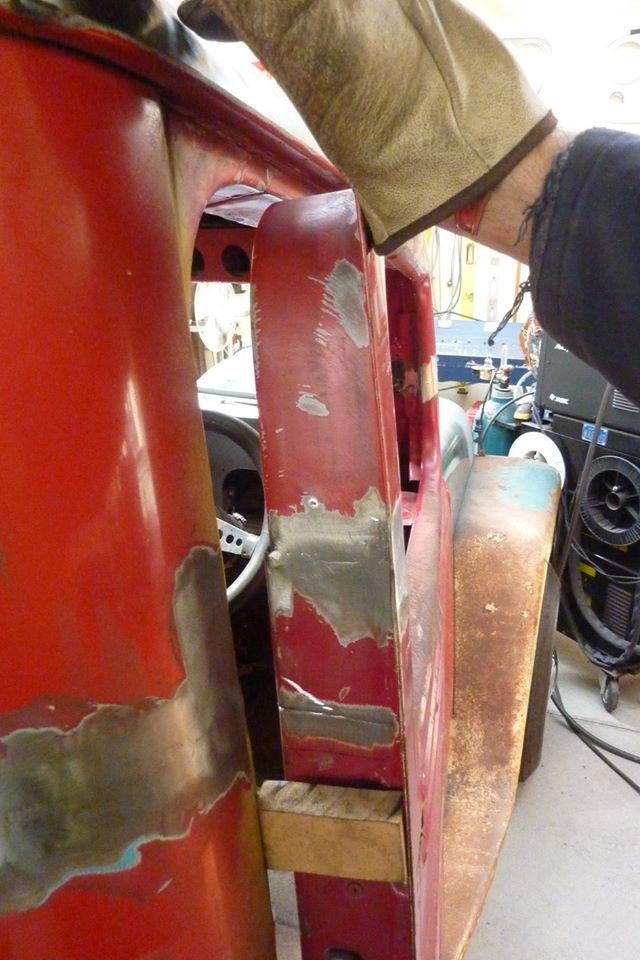
Pushed over and tacked. Then checked to see if it was enough. Remember it will pull a few millimetres more with the weld shrinkage, so allow for that to save stretching the weld afterwards
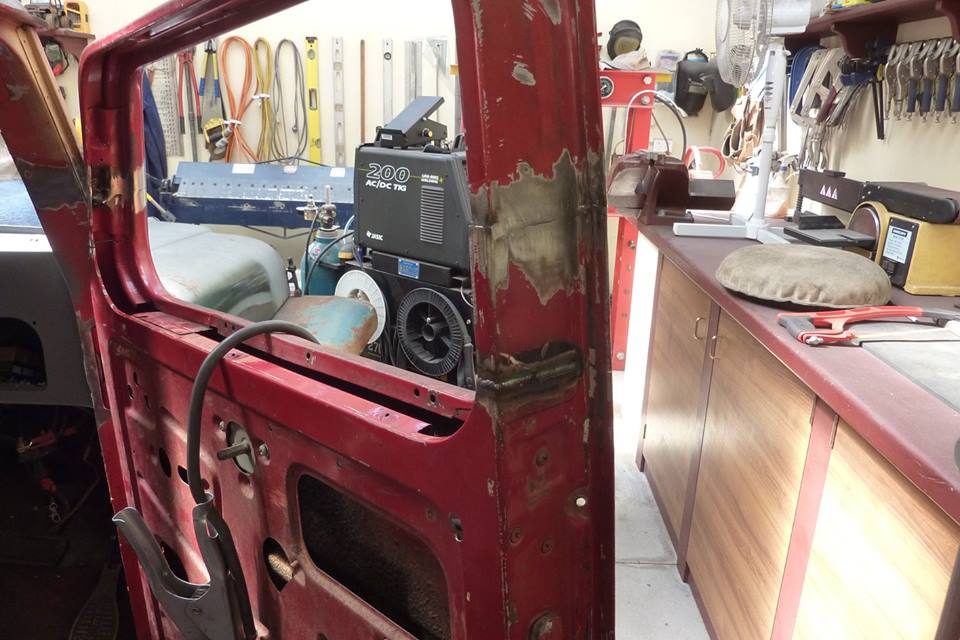
Welded up.
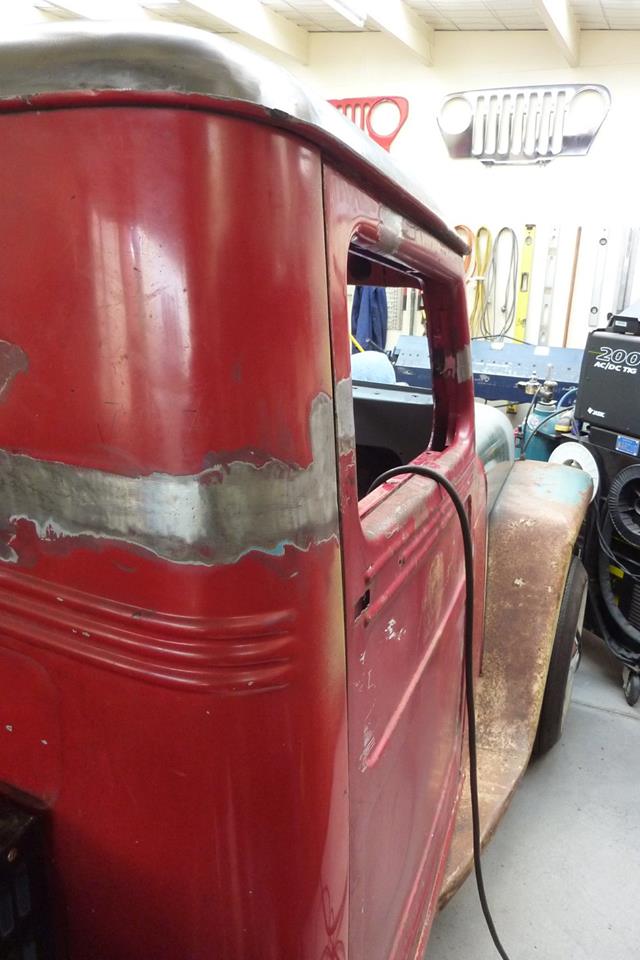
Looks a lot better now.
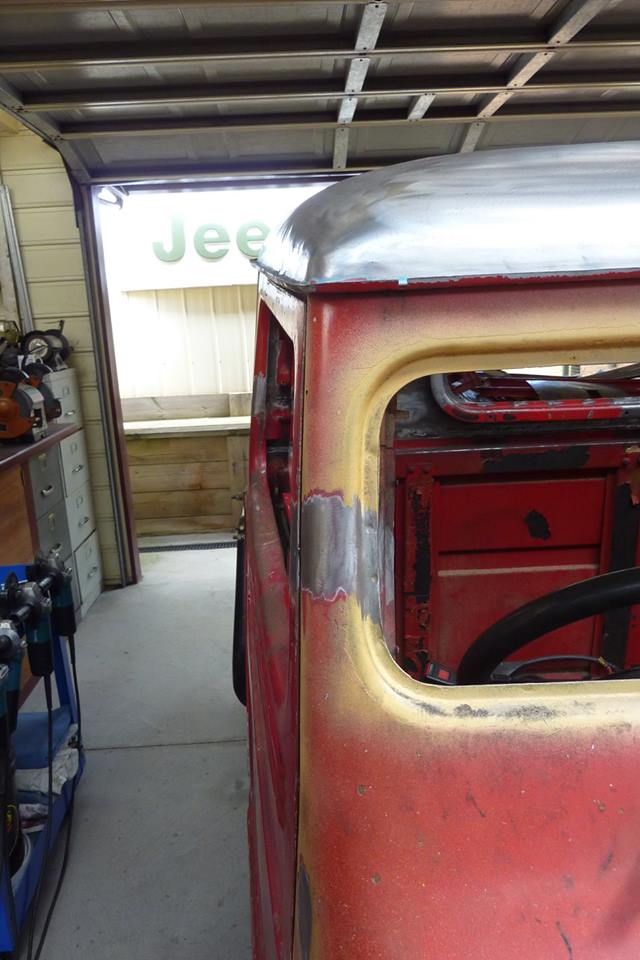
Front was also done.
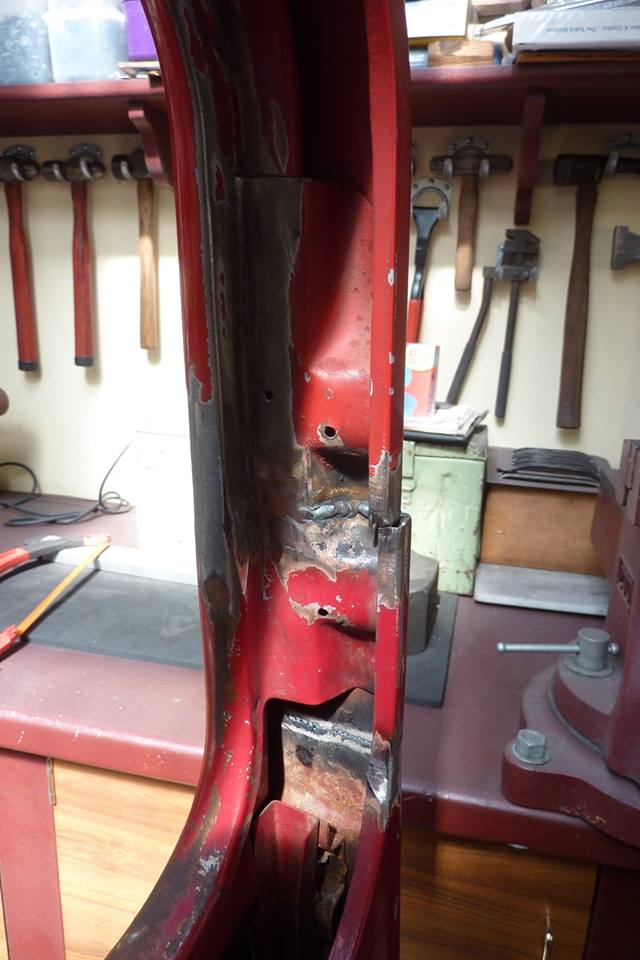
Now this difference in width of the window frame needs to be dealt with. The frame had a slight taper to it so it shows up once the 5.5" was chopped out.
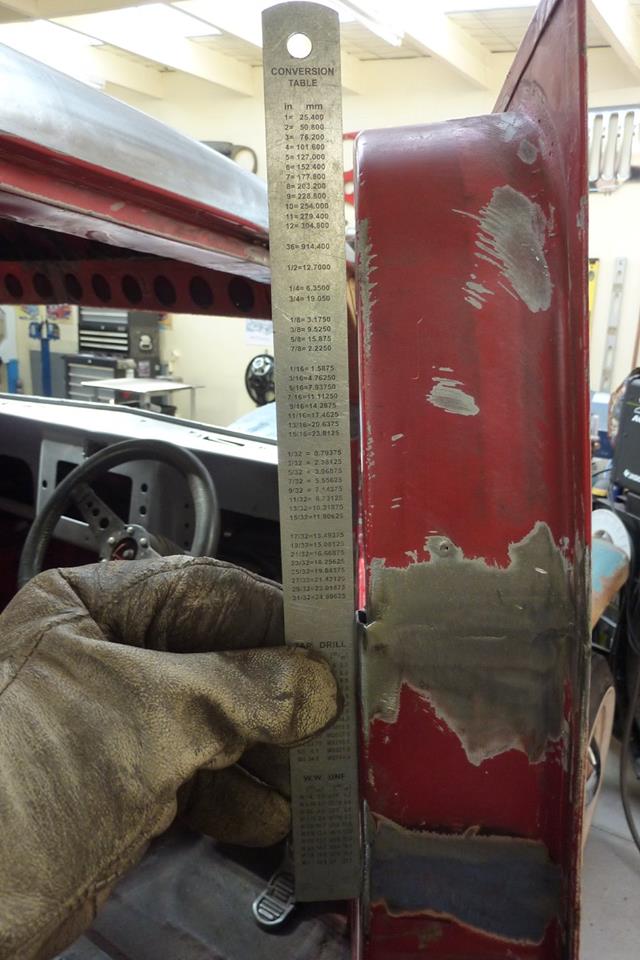
Can see it better from this angle.
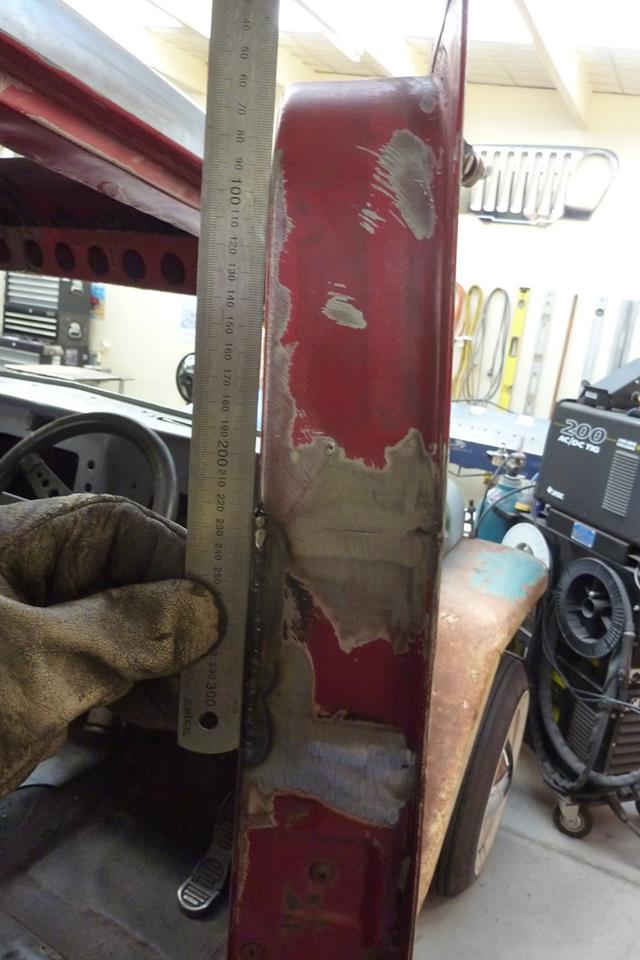
Bottom was cut and then pulled in only to the point where it lined up with the top of the frame. Pulling it to meet the bottom of the upper half would leave a dip which will show up once the straight window surround is against it.
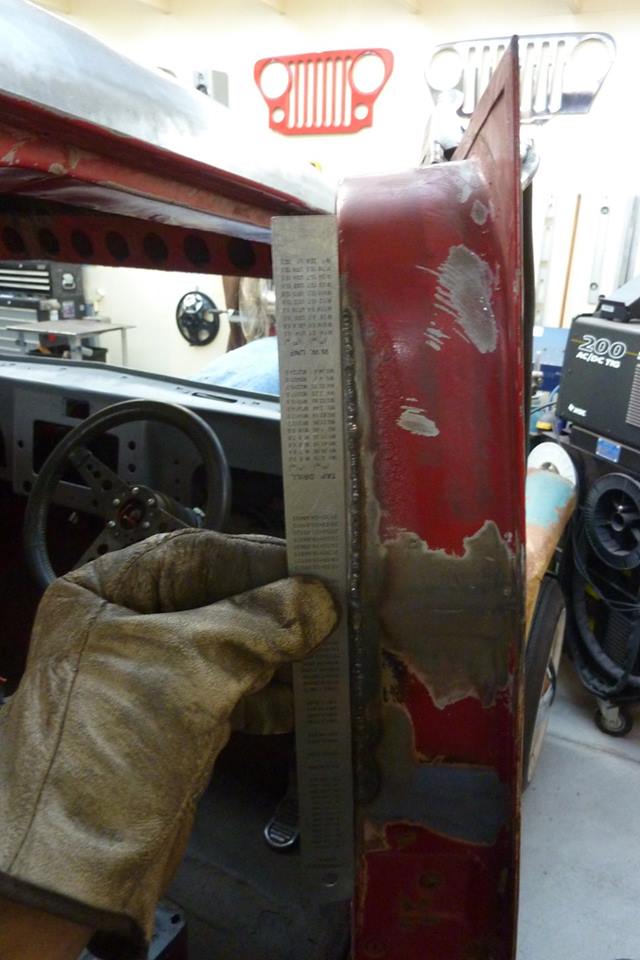
Top half cut and pulled out to meet the lower piece.
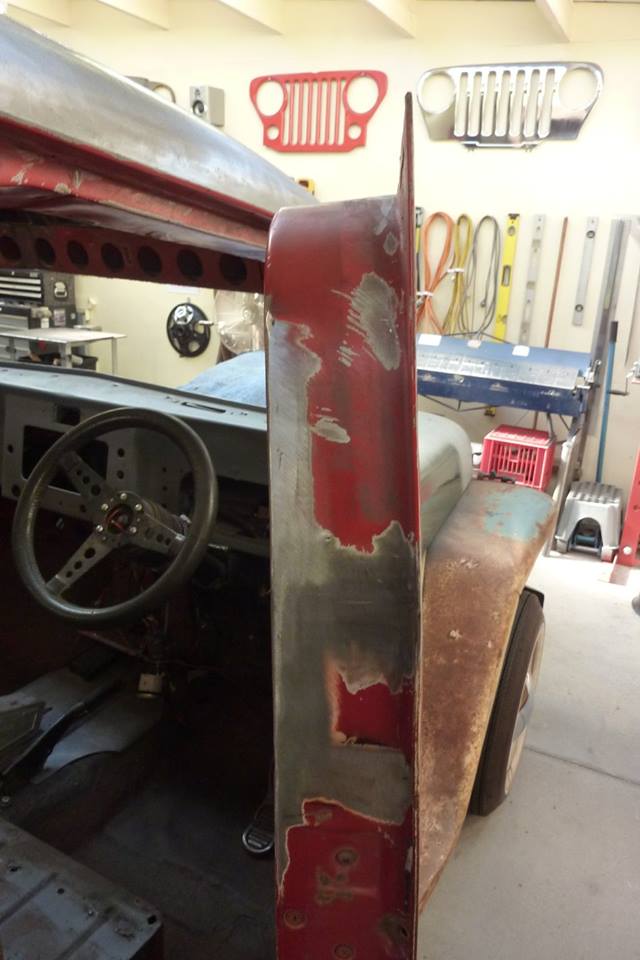
All finished up.
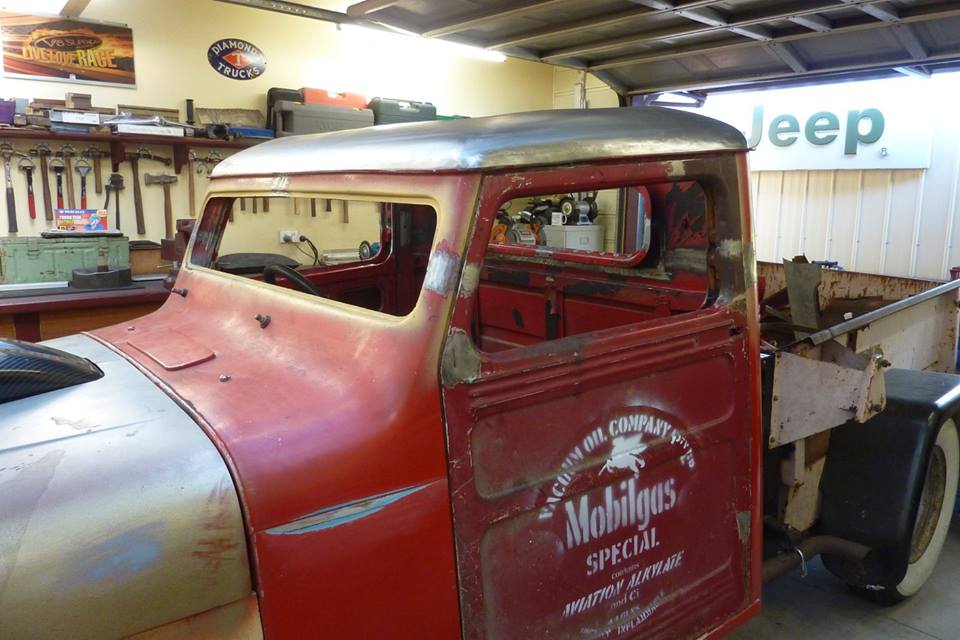
Now in my opinion the height difference between the windscreen and the door window is out of proportion to each other. It is why I sectioned the cab under the windscreen and chopped only the door window 2" to match it up. Unfortunately this only gets worse the bigger the chop if both windscreen and window is cut only such as here.
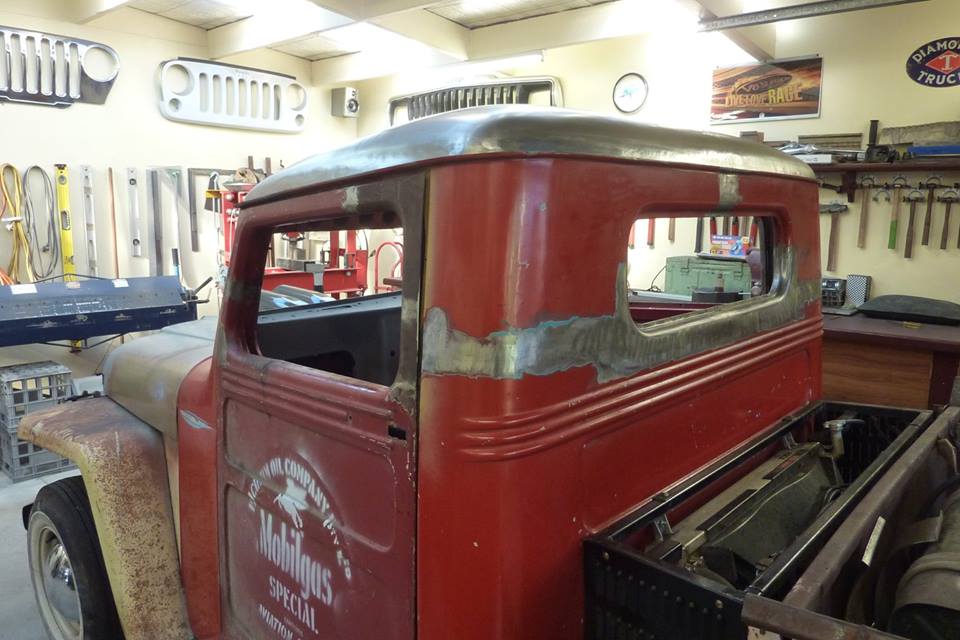
Same from the back view.
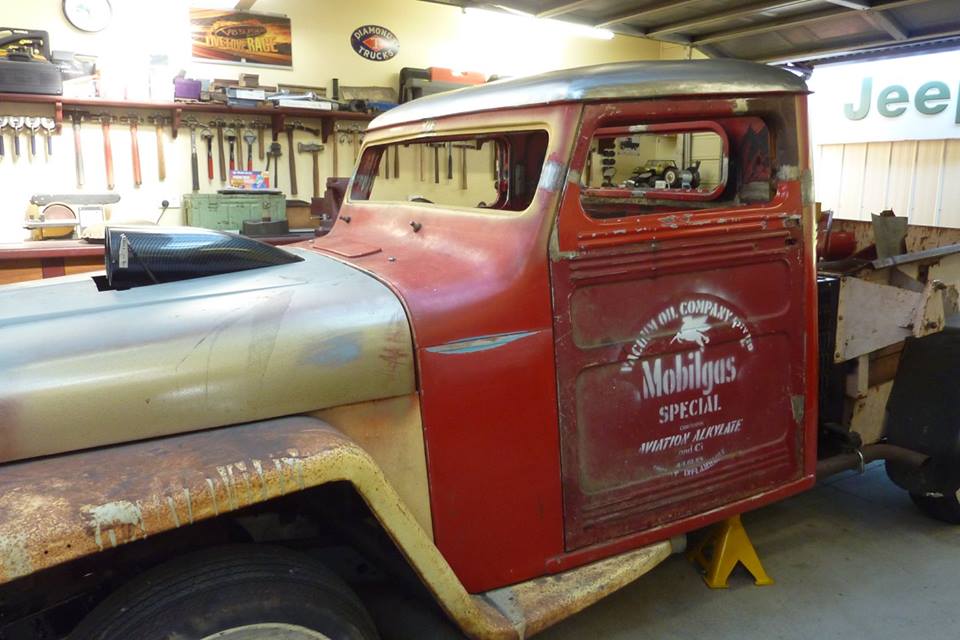
Now I had this idea to solve the problem another way many years ago before I sectioned mine the way I did. That is to raise the window sill instead. This mock up it is raised 50mm or 2" to match the height of the windscreen not including the flanges.
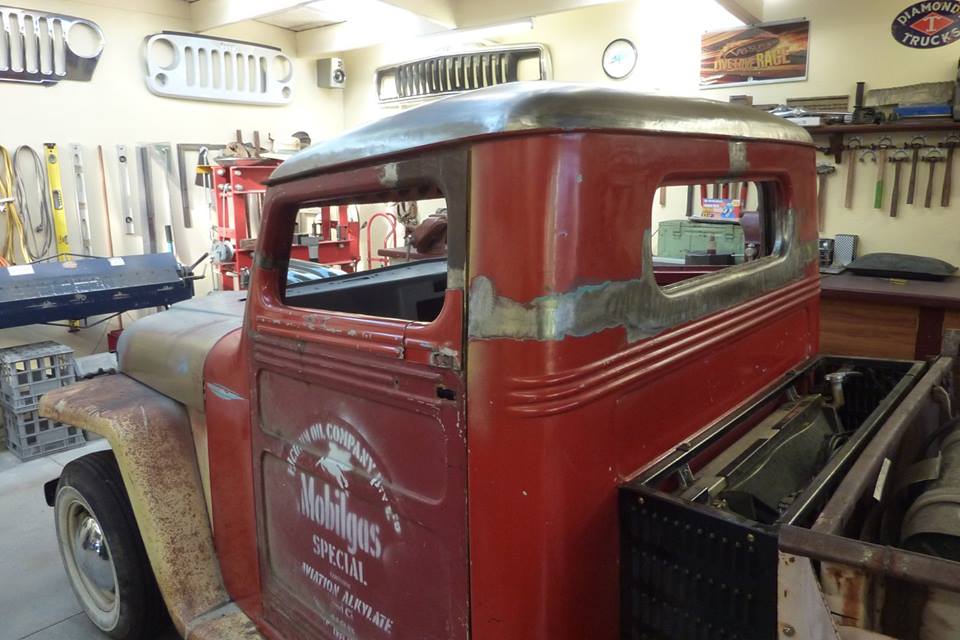
Rear view with 50mm-2" raised window sill.
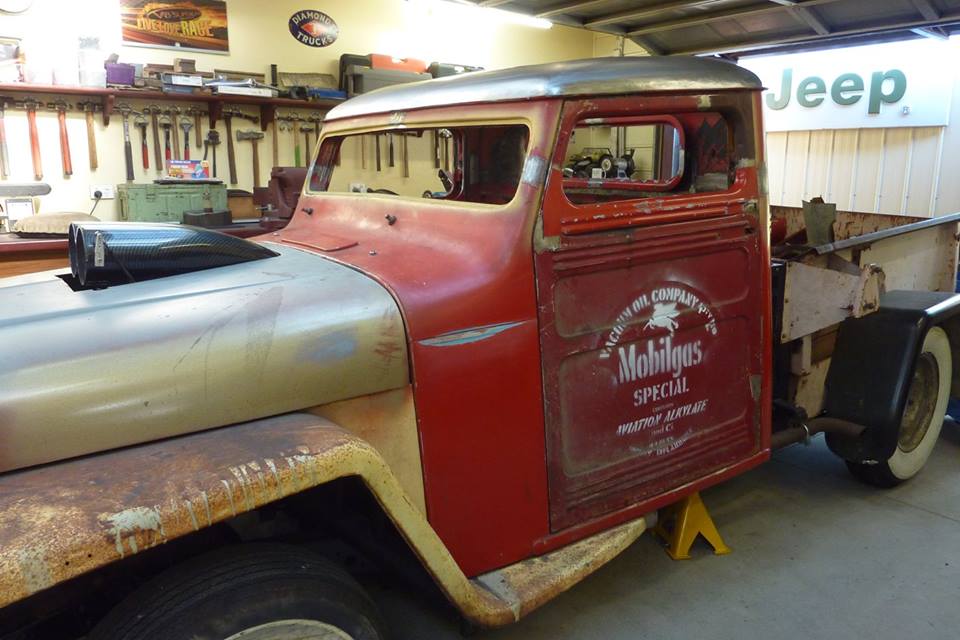
This is 65mm-2.5" which matches the opening of the windscreen including the flanges.
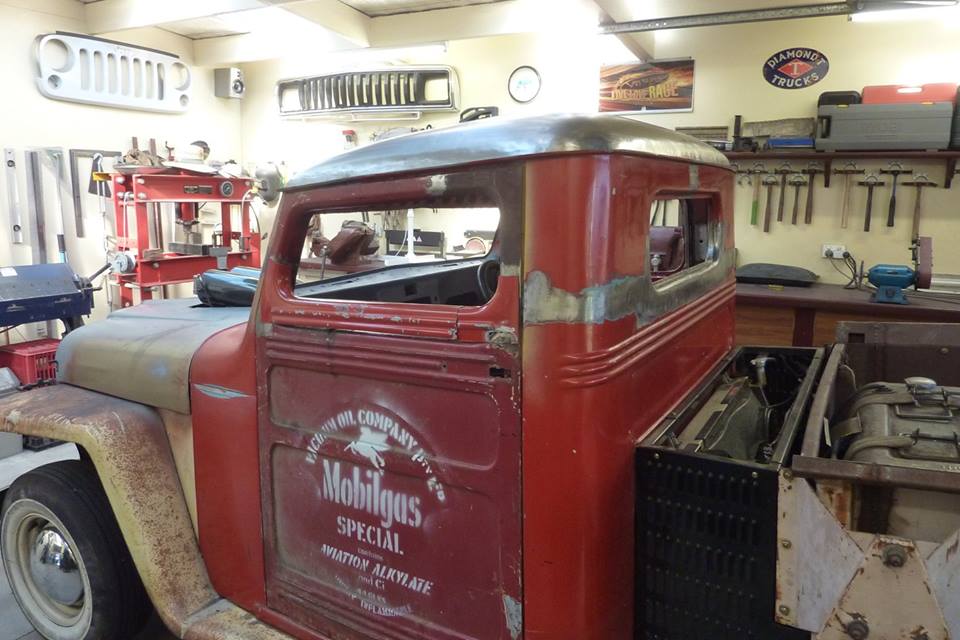
65mm-2.5" raised window sill. The inside frame would have to be raised as well to match of course and would not have the extra ribs. Just a thought anyway.